Custom insulated bearings for electric motors represent a vital advancement in enhancing motor efficiency and longevity. As industries strive to meet higher efficiency standards and reduce operational costs, these specialized bearings play a pivotal role in achieving electrical insulation and mitigating electrical discharge-related damages.
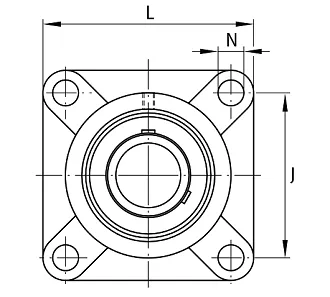
Firstly, understanding the principle behind insulated bearings is crucial. Electric motors, particularly those using variable frequency drives, are prone to electrical discharges across their bearing surfaces. This phenomenon can cause premature bearing failure, resulting in costly downtime and maintenance. Insulated bearings resist these discharges through advanced ceramic coatings or hybrid designs using ceramic rolling elements, effectively enhancing motor reliability.
From an expert perspective, the importance of selecting the appropriate insulated bearing cannot be overstated. Not all motors demand the same type of insulation, and factors such as voltage level, operating environment, and load requirements dictate the choice. Consulting with a bearing specialist is often necessary to customize the solution for specific applications. Custom insulated bearings are tailored to fit specific motor designs and operational protocols, ensuring optimal performance.
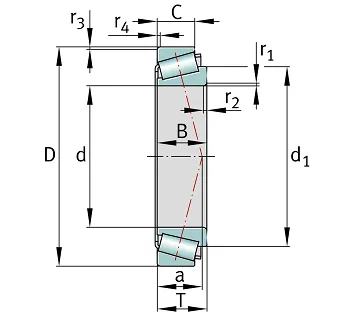
The authoritative insight into the manufacture of custom insulated bearings reveals a meticulous process. Advanced manufacturing facilities utilize state-of-the-art technologies to apply coatings with precision. This precision is essential to maintain balance and minimize vibration. Furthermore, the integration of hybrid ceramic elements offers an additional layer of durability, reducing electrical pitting and wear commonly associated with metal elements. Such technical sophistication in production ensures bearings meet rigorous industry standards, guaranteeing reliable performance in demanding applications.
custom insulated bearings for electric motors
One cannot overlook the trustworthiness factor associated with using custom insulated bearings. Businesses investing in these components benefit from a documented reduction in motor failures associated with electrical discharge damage. Field data and empirical studies consistently show a marked increase in bearing life span and a decrease in maintenance intervals. This not only ensures operational reliability but can also significantly lower long-term operational costs, making a strong case for the adoption of insulated bearing technology.
Real-life case studies further cement the value proposition of custom insulated bearings. Take, for example, a manufacturing plant plagued by frequent motor failures, leading to financial strains due to halted production schedules. Post-implementation of custom insulated bearings, the plant reported a drastic reduction in unplanned downtimes and an extension in the lifespan of their electric motors. Such experiences underscore the indispensable role insulated bearings can play in streamlining operations and boosting productivity.
Additionally, the environmental impact of utilizing custom insulated bearings aligns with contemporary sustainability goals. By prolonging the life of electric motors, industries can significantly cut down on waste and energy consumption associated with manufacturing new motors and components. Therefore, insulated bearings not only aid in reducing operational costs but also contribute positively to a company's ecological footprint.
In conclusion, custom insulated bearings for electric motors are not merely auxiliary components but crucial elements that offer both technical and economic advantages. Their ability to provide superior electrical insulation, when tailored to specific operational needs, makes them an essential asset in modern industrial setups. By leveraging expertise in design and manufacturing, and backed by authoritative data, businesses can trust these bearings to deliver unparalleled performance and reliability.