The manufacturing process of custom ceramic ball bearings represents a fascinating fusion of technology and materials science, which is finely tuned to meet specific industrial needs. The unparalleled precision and resilience of ceramic ball bearings stem from their complex production methods and the inherent properties of the materials used. This article explores the intricate process involved in manufacturing these high-performance components, highlighting key elements that ensure quality and efficiency.
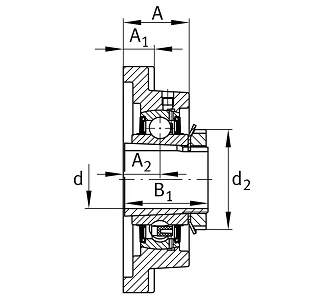
Ceramic ball bearings are primarily composed of silicon nitride, a material known for its high strength and lightweight characteristics. The process begins with the selection of premium raw materials, focused on purity and uniformity to guarantee optimal performance. Knowledgeable experts in material science assess the composition, ensuring that the ceramic powder meets stringent industry standards.
Once the raw materials are approved, they undergo a sophisticated powder processing system. This involves mixing the silicon nitride powder with binding agents and other additives that enhance the material's properties. The blend is then subjected to a high-energy milling process that refines the particle size, ensuring uniformity and improving the mechanical properties of the finished bearing.
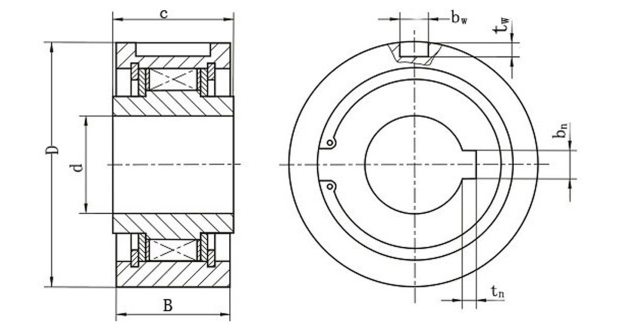
In the subsequent forming stage, the fine powder is shaped into rough spherical forms using advanced pressing techniques. Isostatic pressing is commonly employed, where the powder is compacted under high pressure, ensuring uniform density throughout the material. This method is crucial in eliminating potential weak points that could compromise the integrity of the bearings under stress.
The formed spheres are then headed to a sintering furnace, a critical phase where the green ceramic bodies are heated to temperatures exceeding 1,400 degrees Celsius. This process fuses the particles together, enhancing the mechanical strength, hardness, and wear resistance of the spheres. Precision control of the sintering environment ensures that the microstructure is optimized for durability and efficiency.
custom ceramic ball bearing manufacturing process
Post-sintering, the spheres undergo a grinding process to achieve the desired dimensions and surface finish. This step is performed with high-precision diamond grinding wheels, capable of achieving tolerances within microns. The grinding phase is essential for reducing friction and wear, crucial for applications that demand high-speed and high-durability bearings.
Once the desired specifications are reached, the ceramic balls must undergo meticulous quality control procedures. These include non-destructive testing methods such as ultrasonic inspection and X-ray analysis to detect any internal inconsistencies. Furthermore, dimensional accuracy is verified using coordinate measuring machines, guaranteeing that each bearing meets the highest standards of precision.
As a final step, the ceramic balls are polished to achieve a smooth surface. Polishing enhances not only the aesthetic appeal but also the functional performance, as a smoother surface reduces friction and extends the lifespan of the bearing. This is especially critical in high-performance applications, where even minor imperfections can lead to significant operational issues.
The manufacturing process of custom ceramic ball bearings is a testament to advanced engineering capabilities. Skilled professionals diligently oversee each stage, leveraging state-of-the-art technology to produce bearings that excel in challenging environments. Ceramic ball bearings’ superiority in weight, wear resistance, and thermal stability enables their use in cutting-edge applications across industries like aerospace, automotive, and high-performance machine tools.
By understanding this intricate manufacturing process, industries can better appreciate the value ceramic ball bearings add to their systems and processes. These components epitomize reliability and efficiency, essential traits in today's advanced industrial landscape. Through continuous innovation and expertise, manufacturers ensure that ceramic ball bearings set the benchmark for excellence and performance.