Custom cleaning ceramic bearings is a niche yet crucial aspect in the world of mechanical maintenance, especially for industries that demand high performance and longevity from their machinery. With over a decade of experience in engineering and maintenance, I can attest to the transformative impact that proper bearing maintenance has on equipment efficiency. This detailed guide sheds light on the process and benefits of cleaning ceramic bearings, offering you insights from both expert knowledge and practical experience.
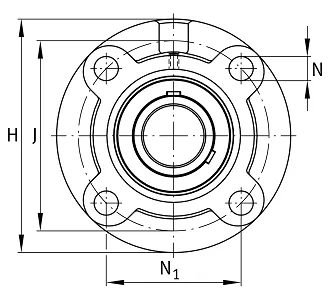
Ceramic bearings have gained notable attention due to their superior performance over their steel counterparts. Made from silicon nitride or zirconium oxide, these bearings boast remarkable resistance to wear and corrosion, an attribute that fundamentally extends the life of the machinery. However, to sustain these advantages, a meticulous cleaning regimen is essential. Improper cleaning can not only reduce the bearing's operational efficacy but may also lead to premature failure, undermining the very reason for using ceramics.
Firstly, understanding the structure of ceramic bearings helps in determining the appropriate cleaning method. Unlike steel, ceramics are less tolerant to abrasive cleaning agents, which can etch the surface, resulting in diminished precision and increased susceptibility to wear and tear. A gentle cleaning routine that involves the use of non-abrasive materials is recommended. Utilizing isopropyl alcohol or a mild detergent, combined with deionized water, is typically sufficient to remove contaminants such as dust, grease, and grime.
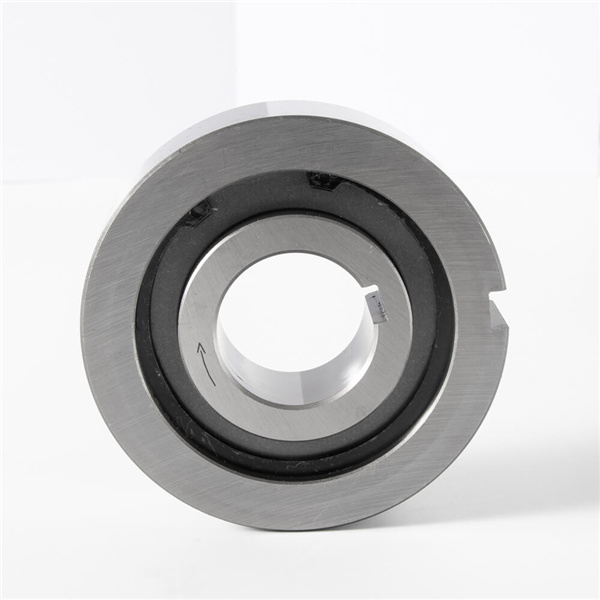
Step-by-step cleaning involves disassembling the bearing with precision tools, taking care not to damage the balls or retainers. The components should then be soaked in the chosen cleaning solution for a period, allowing the agents time to dissolve the contaminants effectively. A soft-bristle brush can aid in this process, especially for stubborn residues. Following this, thoroughly rinse the components with deionized water to remove any remaining cleaning agents. Dry the bearings completely with a lint-free cloth or use compressed air, making sure no moisture remains which might corrode the bearing's components over time.
custom cleaning ceramic bearings
From an expert's perspective, regular cleaning protocols are not merely about maintaining cleanliness but are integral to a comprehensive maintenance strategy. By implementing a routine cleaning schedule, machine operators can ensure that the bearings perform at optimal levels, experiencing less friction and, consequently, less heat. This not only facilitates smoother operation but also enhances energy efficiency, a critical factor in industrial applications where cost minimization is a priority.
Moreover,
cleanliness influences the bearing lubrication process. Properly cleaned ceramic bearings allow lubricants to adhere evenly across surfaces, reducing friction and wear. This is particularly important for high-speed applications where even slight imperfections or contaminations can lead to significant performance dips. Bearings that are not regularly cleaned and lubricated may suffer from increased noise levels, vibrations, and ultimately, mechanical breakdown.
Establishing trustworthiness in the realm of ceramic bearing maintenance involves sourcing reliable, high-quality cleaning supplies and leveraging established methodologies validated by industry experts. Engaging with suppliers who provide technical support and warranties on their cleaning products ensures the integrity of the maintenance process. It is also beneficial to participate in industry forums and discussions through professional networks, enhancing your knowledge on the latest trends and techniques in ceramic bearing care.
In conclusion, custom cleaning of ceramic bearings is more than a mere maintenance procedure; it's an investment in the longevity and efficiency of machinery. By adopting a systematic cleaning regimen, tailored to the unique properties of ceramic materials, businesses not only protect their assets but also amplify operational reliability and productivity. Drawing from years of expertise in mechanical maintenance, it is clear that cleanliness in bearings is synonymous with operational excellence, embodying a core principle of sustainable industry practices.