Custom greasing of electric motor bearings is an essential practice for ensuring the longevity and optimal performance of electric motors, crucial in numerous industrial applications. Precision in this process not only maximizes efficiency but also minimizes downtime, enhances reliability, and prolongs the motor's life.
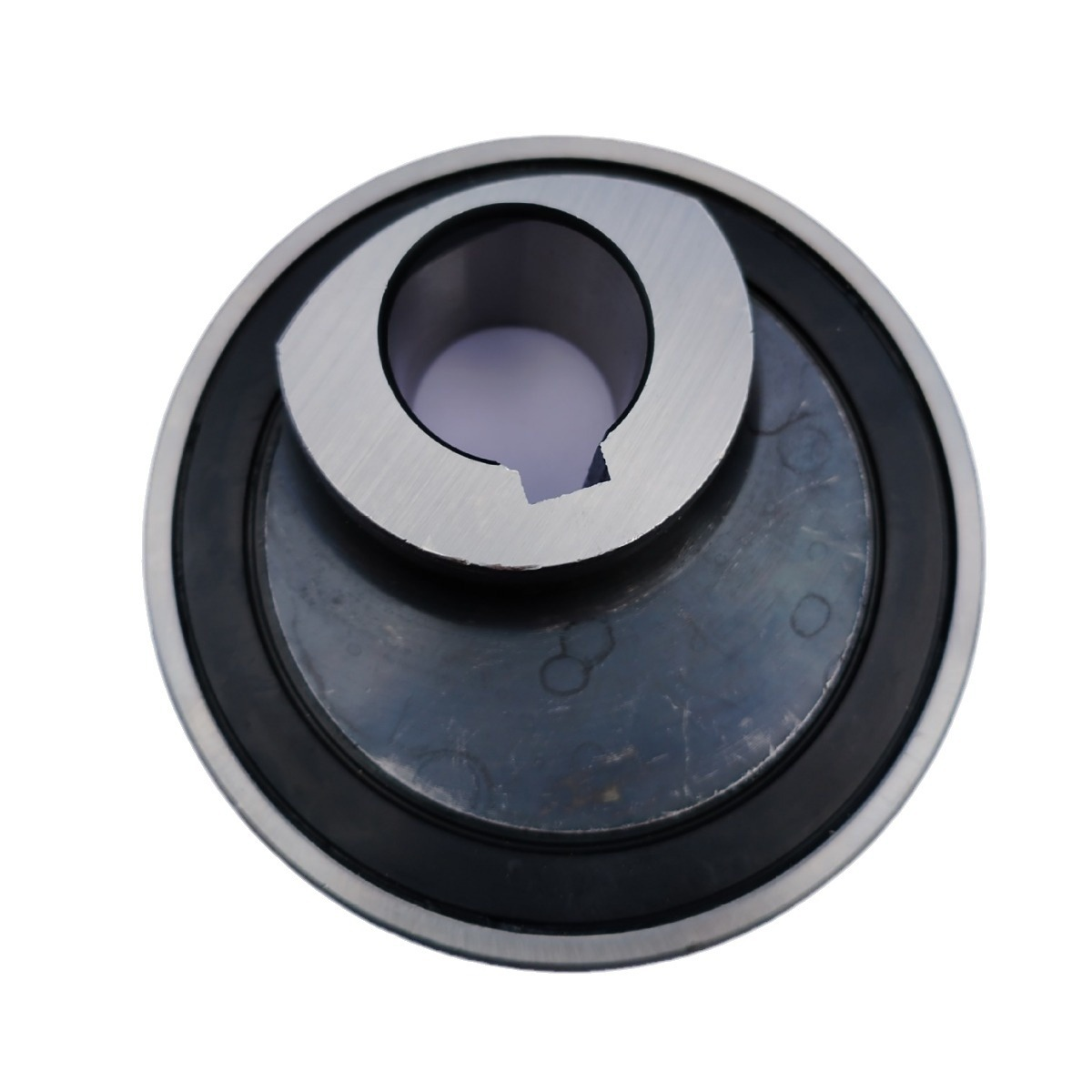
For those with experience in mechanical maintenance, understanding the unique needs of electric motor bearings can significantly contribute to the success of maintenance programs. The most common bearings found in electric motors are ball bearings and roller bearings, and each has specific lubrication requirements that need to be addressed with expertise.
Ball bearings often operate at higher speeds with lower loads. Their lubrication requires a high-quality grease that can reduce friction and prevent overheating.
A proper greasing schedule should be established based on the motor's operating environment and conditions. Over-lubrication or under-lubrication can lead to premature bearing failure, which is why the right balance must be maintained.
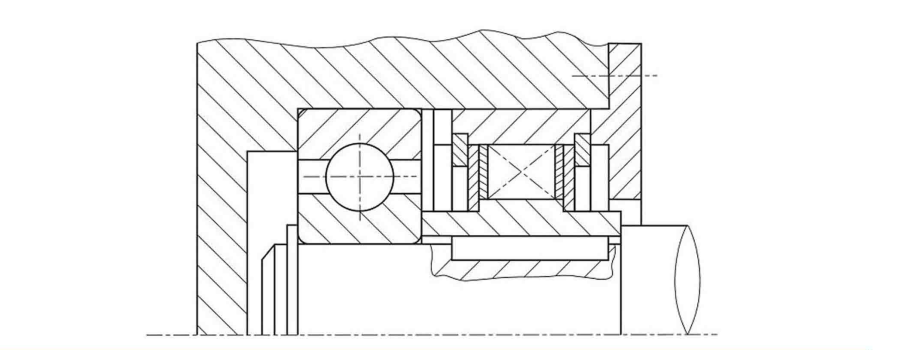
On the other hand, roller bearings are typically used in applications with heavier loads and lower speeds. The greasing intervals for these bearings might differ from ball bearings, requiring greases that can sustain the pressure and temperature variations typical in such settings. A tailored greasing approach ensures that the specific demands of these bearings are met, reducing the risk of mechanical failure. An authoritative understanding of these differences highlights the importance of expertise in custom greasing strategies.
Environmental factors also play a crucial role in determining the type and frequency of greasing. Motors operating in dusty, wet, or chemically active environments may require more frequent greasing or specialized greases that can withstand these harsh conditions. Trustworthy information from manufacturers and seasoned engineers can provide the best guidance for selecting these greases.
custom greasing electric motor bearings
Innovation in grease formulations has given rise to synthetic options that offer superior performance in extreme conditions compared to traditional mineral-based greases. Synthetic greases have higher thermal stability and better performance characteristics, making them ideal for demanding applications. Authoritative resources can help guide decisions around upgrading to synthetic options, providing insights into how these greases extend the service life of motor bearings.
Real-world experience underscores the importance of having a detailed maintenance plan that includes routine inspections and greasing schedules. Catching issues like unusual noises, vibration, or heat can prevent failures. Expertise in using tools like infrared thermography or vibration analysis for early diagnosis complements a robust greasing strategy, ensuring a proactive maintenance regime.
Additionally, ensuring the knowledge and skillset of maintenance personnel is up-to-date with industry standards is vital. Regular training sessions and workshops can equip teams with the latest knowledge and techniques, reinforcing their capability to execute precise greasing techniques.
In conclusion, custom greasing of electric motor bearings, when executed with experience, expertise, authoritativeness, and trustworthiness, can turn routine maintenance into a strategic advantage. Properly lubricated bearings can achieve peak performance and longevity, ultimately enhancing the operational efficiency and reliability of industrial systems. Thus, investing time and resources into understanding and implementing custom greasing practices is an investment into the enduring success of any operation reliant on electric motors.