Finding the perfect component for a mechanical project can be a challenging task, especially when precision and reliability are paramount.
This is often the case when selecting custom deep groove ball bearings specifically designed to fit a 12mm shaft. The pursuit of this ideal component requires not only a deep understanding of engineering principles but also a keen eye for quality and suitability to ensure the smooth operation and longevity of the machinery in question.
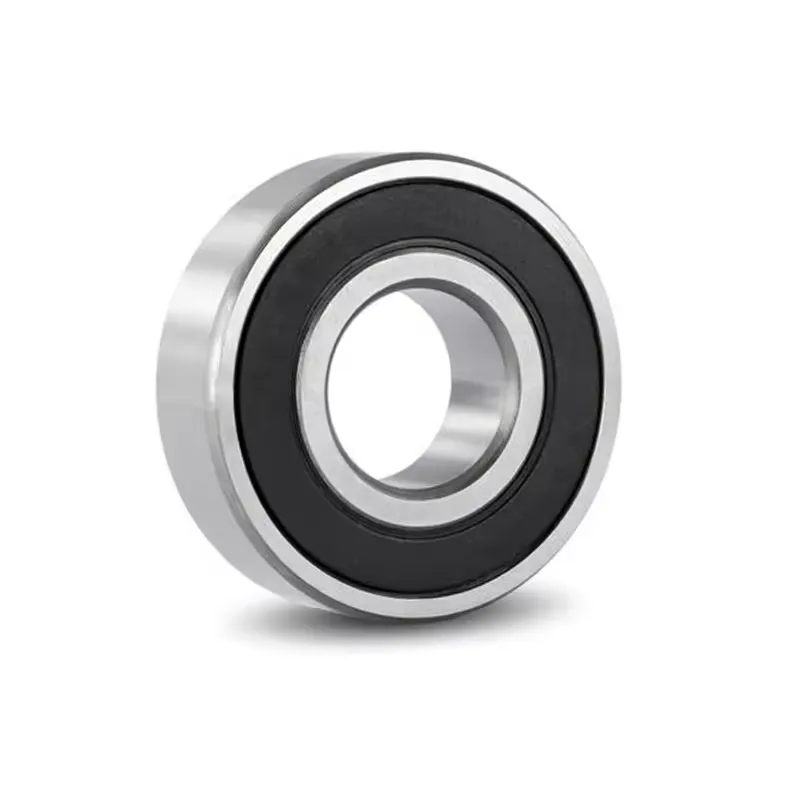
Deep groove ball bearings are renowned for their versatility and are frequently used across various industries due to their ability to handle radial and axial loads efficiently. When deploying them for a 12mm shaft, customization becomes crucial to maximize performance and integrate seamlessly with the surrounding machinery.
One of the critical factors in this process is material selection, which significantly impacts the bearing's endurance and efficiency. High-quality stainless steel is often the material of choice due to its robustness and resistance to corrosion. This not only ensures longevity but also maintains the bearing's integrity under various environmental conditions.
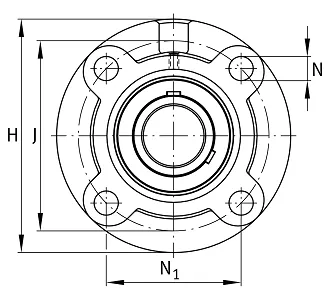
Precision manufacturing is equally important in creating a custom deep groove ball bearing. The slightest deviation in size or shape can lead to mechanical failures, making the certification and quality assurance processes vital. Manufacturers employ advanced computer-aided design (CAD) and precision machining tools to craft bearings that align perfectly with a 12mm shaft, promising a flawless fit and enhanced performance.
The lubrication process is another pivotal aspect of ensuring the bearing's optimal function. Proper lubrication reduces friction and wear, guaranteeing smoother rotations and extending the bearing's lifespan. Depending on the operational environment, selecting the appropriate grease or oil can dramatically increase efficiency and reduce maintenance costs.
custom deep groove ball bearing to fit a 12mm shaft
While focusing on customization, it is essential to consider the installation process. Incorrect installation can lead to premature bearing failure. Techniques such as using the correct mounting tools and adhering to specified torque levels prevent misalignment and undue stress on the bearings, enabling them to perform under intended operational loads accurately.
Customer testimonials often highlight the importance of working closely with suppliers who offer customization services and technical support. A reliable supplier not only provides high-quality bearings but also offers guidance through the selection and installation process. This collaborative approach ensures that the bearings meet all specific project requirements and contribute to the machinery's overall effectiveness.
Industry experts emphasize regular maintenance checks post-installation to detect early signs of wear or failure. Incorporating monitoring tools and predictive maintenance strategies significantly reduces downtime and operational costs, thereby increasing the return on investment for customized components.
Research and development in the sphere of deep groove ball bearings are continually advancing, with innovations in materials and designs consistently emerging. Engaging with reputable manufacturers who stay at the forefront of these trends guarantees that your machinery benefits from the latest technological advancements.
In essence, the process of selecting a custom deep groove ball bearing for a 12mm shaft is multi-faceted, requiring a blend of expert knowledge, precise engineering, and trustworthy manufacturing practices. By prioritizing these elements, businesses can ensure that their mechanical systems function at peak performance, providing both competitive advantages and operational reliability.