Sealed Spherical Roller Bearings A Comprehensive Look into their Manufacturing
Sealed spherical roller bearings, an innovative engineering marvel, have revolutionized the world of machinery and equipment. These bearings, with their unique design and exceptional performance, are manufactured by a select few specialized companies globally. This article delves into the intricacies of sealed spherical roller bearings' manufacturing process, their significance, and the manufacturers leading the industry.
Spherical roller bearings, as the name suggests, feature a spherical outer ring raceway, allowing them to accommodate not only high radial loads but also substantial axial loads in either direction. The addition of a sealing mechanism elevates their functionality, protecting the internal components from dust, moisture, and other contaminants, thereby extending their service life.
The manufacturing process begins with the selection of high-quality raw materials, typically bearing steel, known for its durability and wear resistance. The steel is then heat-treated to enhance its mechanical properties. Next, the races and rollers are precisely machined to achieve the required tolerances, ensuring smooth rotation and minimal friction.
Seals play a crucial role in sealed spherical roller bearings. They are made from materials like rubber or polyurethane, offering a balance between flexibility, durability, and sealing efficiency. The seals are carefully integrated into the bearing design, preventing ingress of contaminants while allowing for lubricant retention. Some manufacturers even use labyrinth seals for added protection Some manufacturers even use labyrinth seals for added protection
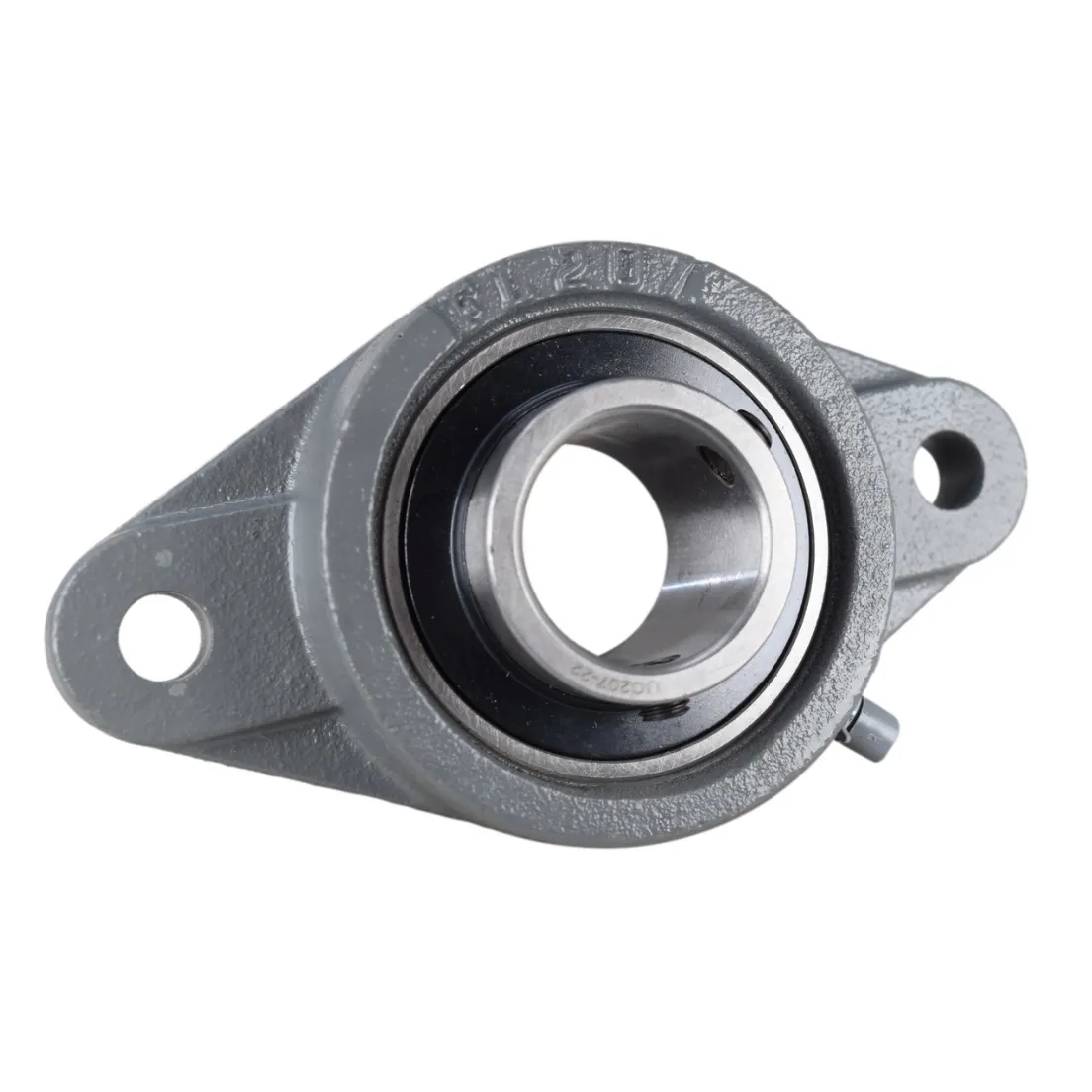
Some manufacturers even use labyrinth seals for added protection Some manufacturers even use labyrinth seals for added protection
sealed spherical roller bearings manufacturer.
Manufacturers such as SKF, Timken, and NSK, among others, are at the forefront of sealed spherical roller bearings production. These companies invest heavily in research and development, constantly refining their manufacturing techniques to improve bearing performance and reliability. Their state-of-the-art facilities employ advanced CNC machines, automated assembly lines, and rigorous quality control measures to ensure every bearing meets stringent standards.
The benefits of sealed spherical roller bearings are numerous. Their ability to handle heavy loads, coupled with their self-aligning feature, makes them ideal for applications in industries like mining, construction, and power generation. The sealed design reduces maintenance needs, lowers downtime, and enhances overall operational efficiency.
In conclusion, sealed spherical roller bearings, a product of meticulous engineering and manufacturing prowess, have proven to be indispensable in modern industrial settings. The dedication of manufacturers to innovate and improve these bearings underscores their commitment to providing solutions that withstand harsh conditions and deliver consistent performance. As technology advances, we can expect even more sophisticated and efficient sealed spherical roller bearings to emerge, shaping the future of engineering and machinery.