The Art and Science of Spherical Bearing Design Manufacturers' Perspective
In the realm of engineering, spherical bearings have emerged as a critical component, providing exceptional precision, stability, and load-bearing capacity in various industries. These innovative devices are designed to minimize friction, ensure smooth rotation, and maintain alignment, making them indispensable in applications ranging from aerospace to automotive, robotics, and heavy machinery.
Spherical bearings, often referred to as spherical roller bearings, owe their name to the presence of (roller) that rest on a spherical raceway, which allows for a unique combination of radial and axial loads. The design principle behind these bearings lies in the spherical shape, which distributes the load evenly, thereby reducing stress and wear. This feature is particularly crucial in high-precision systems where accuracy and longevity are paramount.
Manufacturers of spherical bearings, such as SKF, FAG, NTN, and NSK, employ state-of-the-art technologies and rigorous quality control processes to produce these components. They invest heavily in research and development to enhance the bearing's performance, including optimizing materials like high-strength steel, chrome steel, or even ceramic options for enhanced durability and resistance to corrosion.
The manufacturing process involves meticulous steps, starting with the casting of the inner and outer rings, followed by the grinding and precision finishing of the spherical surface. Each roller is then carefully selected and assembled, ensuring a precise fit within the raceway. Rigorous testing, both static and dynamic, is conducted to verify the bearing's operational characteristics, such as stiffness, speed capabilities, and thermal stability Rigorous testing, both static and dynamic, is conducted to verify the bearing's operational characteristics, such as stiffness, speed capabilities, and thermal stability
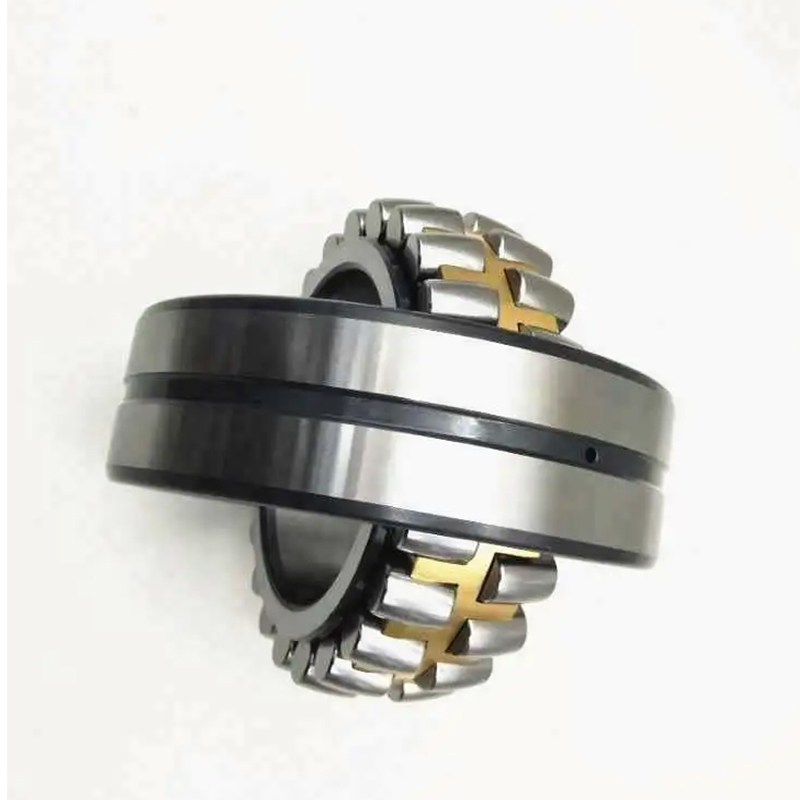
Rigorous testing, both static and dynamic, is conducted to verify the bearing's operational characteristics, such as stiffness, speed capabilities, and thermal stability Rigorous testing, both static and dynamic, is conducted to verify the bearing's operational characteristics, such as stiffness, speed capabilities, and thermal stability
spherical bearing design manufacturer.
One key aspect manufacturers focus on is customization. Spherical bearings can be tailored to meet specific application requirements, with features like different roller sizes, contact angles, and preload settings. This flexibility allows them to cater to diverse industries, from the demanding conditions of oil and gas exploration to the stringent requirements of medical equipment.
Despite the technological advancements, the design and manufacturing of spherical bearings also face challenges, such as managing thermal expansion, maintaining dimensional accuracy, and addressing environmental factors like humidity and temperature. However, dedicated manufacturers continue to push boundaries, leveraging advanced materials and computational fluid dynamics to optimize performance and efficiency.
In conclusion, spherical bearing design manufacturers play a pivotal role in driving innovation and reliability in modern engineering. Their expertise, combined with relentless pursuit of excellence, ensures that these bearings continue to revolutionize the way machines operate, contributing to the seamless functioning of complex systems across industries worldwide. As technology advances, so does the sophistication of spherical bearing designs, promising an exciting future for this essential engineering component.