The Evolution and Significance of Custom Deep Groove Ball Bearings in Modern Industry
In the realm of modern machinery and equipment, custom deep groove ball bearings have emerged as a crucial component that facilitates smooth and efficient rotational movements. These specialized bearings are designed with deeper than standard grooves to accommodate more balls, which significantly enhances their load-carrying capacity and performance under various operating conditions.
Custom deep groove ball bearings are engineered to meet specific requirements of different industries. For instance, in high-speed applications such as dental drills or machine tool spindles, these bearings ensure minimal friction and heat generation, thereby extending the lifespan of the equipment. Moreover, in heavy-duty scenarios like automotive wheel hubs or conveyor systems, they provide superior durability and resistance against shock loads.
The design process of these bearings is meticulous, taking into account factors such as material selection, dimensional tolerances, and lubrication needs. Manufacturers often use high-quality steel for the balls and races, which is then precision-hardened to withstand wear and tear. In addition, the use of advanced elastohydrodynamic lubrication models allows designers to optimize the contact angles and ball sizes for maximum efficiency.
One notable advantage of custom deep groove ball bearings is their ability to handle both radial and axial loads due to their structural design. This versatility makes them ideal for complex mechanisms where space is limited, such as robotic arms or aerospace components This versatility makes them ideal for complex mechanisms where space is limited, such as robotic arms or aerospace components
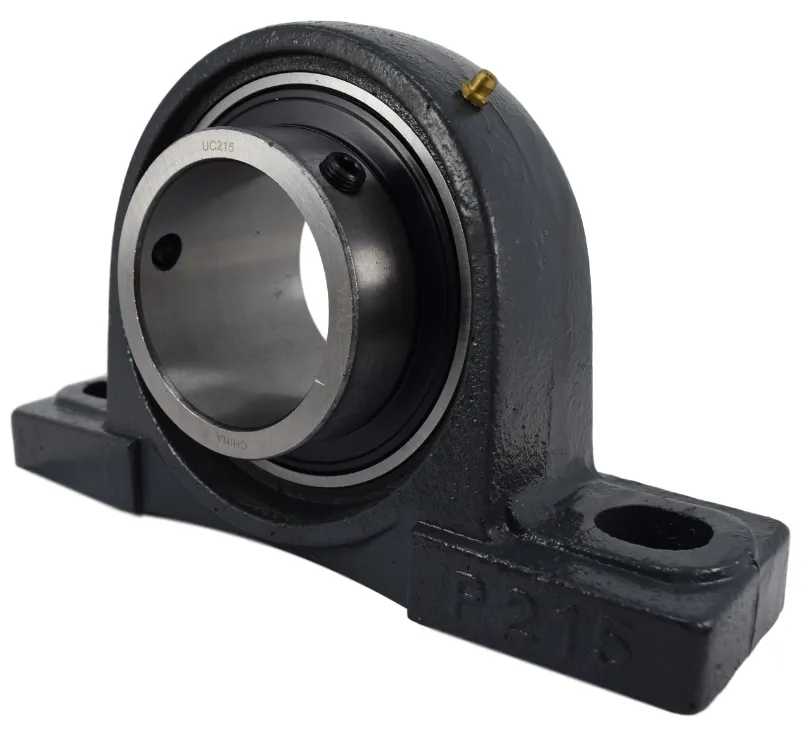
This versatility makes them ideal for complex mechanisms where space is limited, such as robotic arms or aerospace components This versatility makes them ideal for complex mechanisms where space is limited, such as robotic arms or aerospace components
custom deep groove ball bearings. Their compact size and preloadability also contribute to precise positioning and control, essential in high-precision technologies.
Furthermore, the customization aspect ensures that these bearings can be tailored to unique operational environments. For example, in marine applications where corrosion resistance is paramount, stainless steel construction can be specified. Similarly, for food processing equipment where hygiene standards are stringent, non-corrosive and easy-to-clean materials can be used.
In conclusion, custom deep groove ball bearings represent a significant advancement in bearing technology. Their ability to adapt to diverse industrial demands while maintaining high performance has made them indispensable in numerous sectors. As technology continues to evolve, so too will the innovations in custom deep groove ball bearings, ensuring that they remain at the forefront of mechanical excellence and reliability.