Bulk Manufacturing of Ceramic Bearings Precision Engineering at its Finest
In the realm of precision engineering, ceramic bearings have emerged as a game-changer due to their exceptional performance and durability. As the demand for these high-tech components surges, bulk manufacturers are stepping up to meet this challenge with innovative manufacturing processes that balance efficiency, quality, and scalability.
Ceramic bearings, composed primarily of silicon nitride or zirconia, offer numerous advantages over traditional steel bearings. They are lighter, harder, and more resistant to corrosion, leading to enhanced speed capabilities, reduced friction, and increased service life. This makes them ideal for use in various industries, from aerospace and automotive to medical devices and high-performance sports equipment.
Bulk manufacturing of ceramic bearings requires a meticulous approach. The process begins with the production of the bearing balls, which are crafted through a combination of advanced technologies. This includes powder metallurgy, where ceramic powders are formed into shapes, followed by sintering to create a solid structure. The balls are then ground and polished to achieve the required level of precision, often to within microns.
The next step is the production of the bearing races, typically made from high-grade steel to withstand the pressure exerted by the ceramic balls. These are machined with extreme accuracy to ensure a perfect fit with the ceramic elements. The assembly process, though automated for bulk production, demands a keen eye for detail, as even the slightest misalignment can compromise the bearing's performance The assembly process, though automated for bulk production, demands a keen eye for detail, as even the slightest misalignment can compromise the bearing's performance
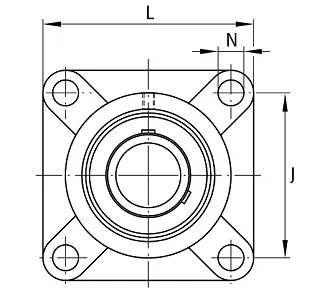
The assembly process, though automated for bulk production, demands a keen eye for detail, as even the slightest misalignment can compromise the bearing's performance The assembly process, though automated for bulk production, demands a keen eye for detail, as even the slightest misalignment can compromise the bearing's performance
ceramic bearings bulk manufacturers.
Quality control is paramount in bulk manufacturing. Each ceramic bearing undergoes rigorous testing, including dimensional checks, hardness tests, and run-out tests to verify concentricity. This ensures that every unit leaving the factory meets stringent industry standards and performs reliably under various operating conditions.
Bulk manufacturers also invest heavily in research and development to continually improve ceramic bearing technology. This includes exploring new materials, coatings, and designs to enhance load-bearing capacity, reduce noise, and increase thermal stability. Such innovations not only cater to the evolving needs of customers but also contribute to the overall advancement of the industry.
In conclusion, bulk manufacturing of ceramic bearings is a testament to the fusion of cutting-edge technology, precision engineering, and industrial scalability. It is a delicate balance between mass production and maintaining the highest levels of quality and performance. With the increasing demand for high-performance components, ceramic bearing manufacturers are poised to play a pivotal role in shaping the future of various sectors, propelling us towards a world of enhanced efficiency and durability.