The manufacturing process of discount ceramic ball bearings is a topic of interest for those seeking high-performance yet cost-effective components in various mechanical applications. This article explores the intricate journey from raw material selection to the final product, emphasizing the expertise and technical craftsmanship involved.
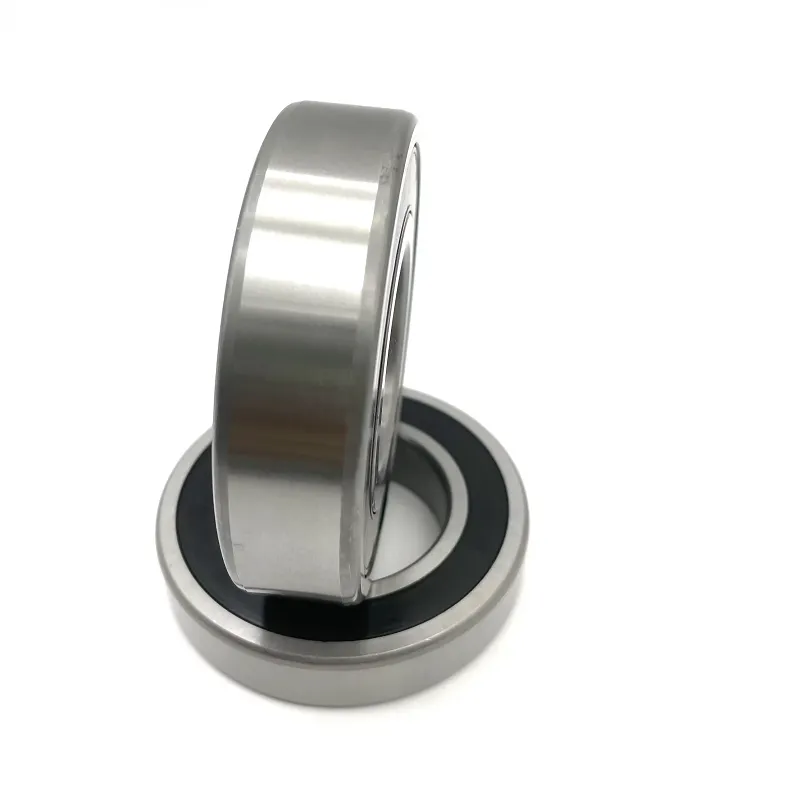
At the heart of any ball bearing manufacturing process is the selection of suitable materials. The process begins with the careful choice of high-quality ceramic materials, known for their incredible hardness, low density, and superior thermal and corrosion resistance. These properties make ceramic bearings ideal for high-speed and extreme-temperature applications.
Ceramics typically used are silicon nitride or zirconia due to their outstanding mechanical properties and reliability. Once the choice of material is finalized, the next step involves powder preparation, which is a crucial stage in ensuring the uniformity and quality of the bearings. The raw ceramic powders are blended to achieve a fine, consistent mixture that meets the specified chemical and physical metrics.
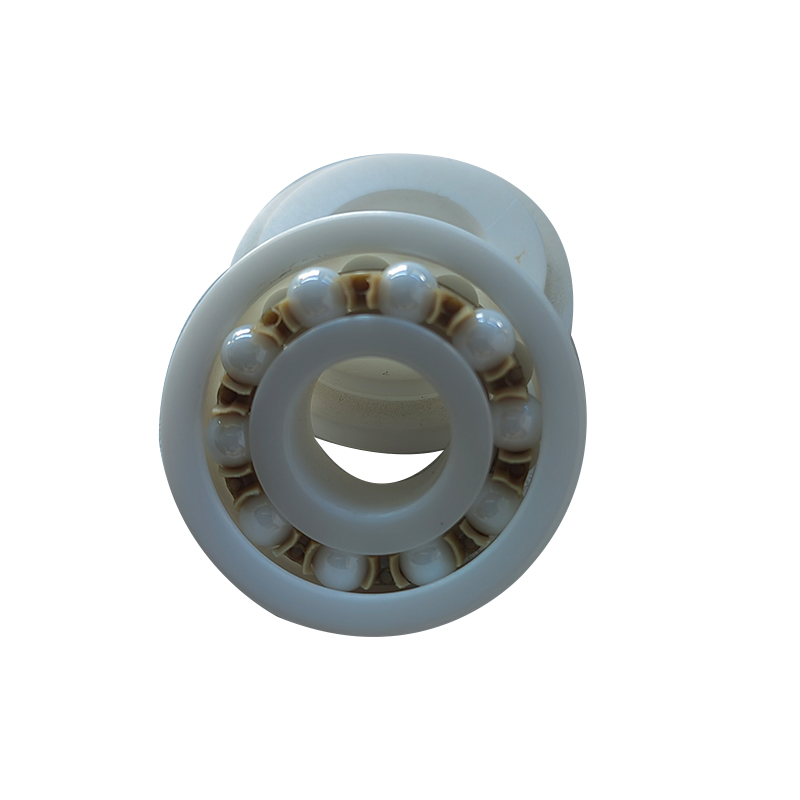
Following powder preparation, the materials undergo shaping processes. This usually involves isostatic pressing or injection molding, which shapes the ceramic powders into green compacts that are slightly larger than the final dimensions to account for shrinkage during sintering. This stage requires meticulous attention to detail to maintain the tight tolerances needed for efficient performance.
The green compacts are then subjected to a sintering process, a thermal treatment that facilitates the densification of the material, improving mechanical strength and integrity. Sintering is typically performed in a high-temperature atmosphere, sometimes in the presence of a vacuum or inert gas, to prevent contamination and achieve desirable microstructural properties. The sintering parameters, such as temperature and holding time, are critical and tailored specific to the ceramic material used.
After sintering, precision machining is employed to achieve the exact dimensions and surface finish necessary for optimal bearing performance. This stage encompasses grinding and lapping, which are executed with high precision equipment. Ceramic materials, due to their hardness, present unique machining challenges that require specialized diamond tooling and advanced machining techniques to achieve the desired level of accuracy.
discount ceramic ball bearing manufacturing process
The final product is then assembled. This involves pairing the ceramic balls with either ceramic or metal races, ensuring minimal friction and optimal load distribution. During assembly, each component undergoes rigorous inspection, including dimensional checks and surface finish assessments, to ensure adherence to stringent industry standards.
Quality assurance is a fundamental characteristic of the discount ceramic ball bearing manufacturing process. Bearings are subjected to extensive testing, including noise and vibration testing, to certify that each unit operates quietly and efficiently under the specified conditions. Traceability of each component within the manufacturing process further enhances trust and reliability, providing customers with transparency about the products they receive.
In contemporary industry practices, manufacturers often emphasize sustainable and cost-effective approaches to production, which is reflected in the efficient use of materials and energy throughout the manufacturing process. By focusing on waste reduction and energy management, manufacturers not only produce more affordable ceramic ball bearings but also contribute to environmentally responsible production methods.
The expertise required in ceramic ball bearing production is indicative of its authoritative standing within the manufacturing sector. This manufacturing process synthesizes material science, precision engineering, and quality control, ensuring that each ceramic bearing meets the high performance and durability demands expected of them.
This comprehensive understanding of the manufacturing process underscores the trustworthiness and reliability that consumers associate with discount ceramic ball bearings. By adhering to these expert-driven manufacturing principles, producers ensure their place within the competitive landscape, providing top-tier solutions at an affordable price point without compromising on quality.