In the realm of modern engineering, custom heavy duty spherical bearings play a pivotal role in enhancing machinery performance and longevity across a spectrum of industries. These specially designed components are not merely off-the-shelf items but are tailored solutions engineered to meet the rigorous demands of heavy-duty applications. This article delves into the unique advantages of these custom solutions, underscoring their invaluable contributions to engineering and manufacturing sectors.
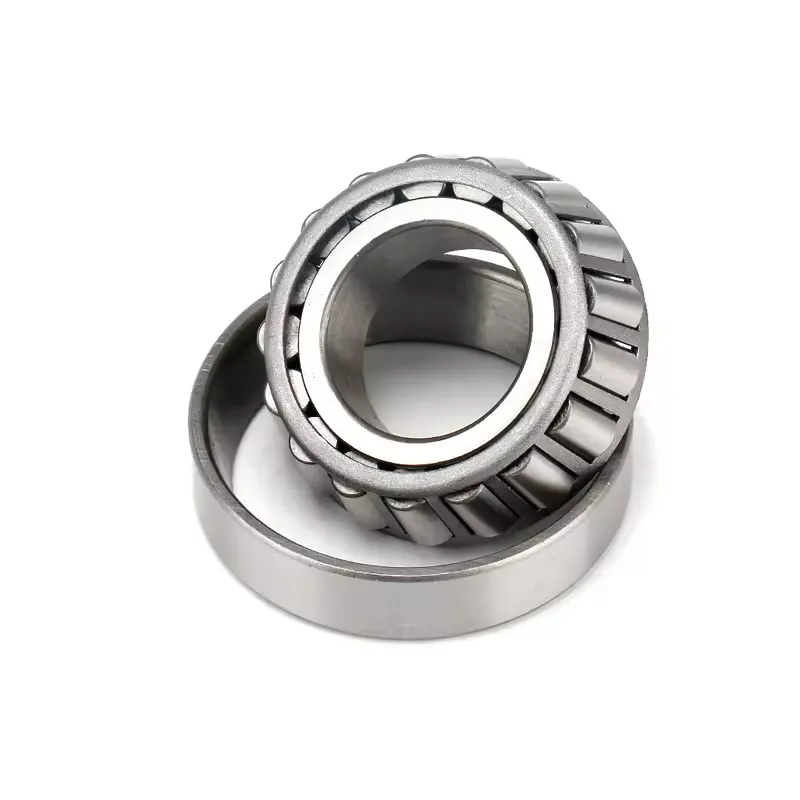
Spherical bearings are a fascinating piece of engineering. Their design allows for angular rotation around a central point, which makes them ideal for accommodating misalignment and axial loads.
When moving into heavy-duty territory, the challenge is amplified. Machines in industries such as mining, construction, and aerospace often operate under severe conditions, where high loads, extreme temperatures, and harsh environments are the norm. Standard bearings would quickly fail under such stress, leading to costly downtime and frequent replacements. This is where custom heavy duty spherical bearings come into play, providing a lifeline for smooth and continuous operations.
One of the preeminent benefits of custom spherical bearings is their adaptability. Tailored to the unique specifications of a given application, these bearings offer enhanced performance and reliability. Engineers and manufacturers collaborate to design solutions that incorporate the specific load-bearing requirements, material specifications, and environmental conditions of their application. For instance, in corrosive environments, bearings can be constructed from specialized alloys or treated with surface coatings to resist wear and corrosion, significantly extending their operational life.
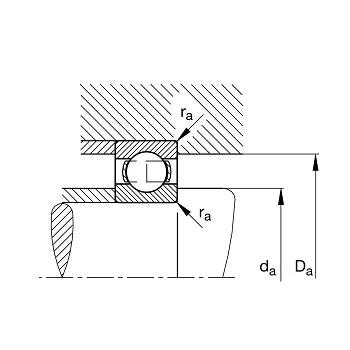
Another key advantage lies in precision engineering and manufacturing. By leveraging advanced design tools and manufacturing techniques, today’s bearing manufacturers can create products that meet exacting standards of tolerances and durability. The expertise involved in crafting these components is substantial, involving a deep understanding of material science, load dynamics, and mechanical design. Such high-level engineering ensures that each bearing can withstand the bespoke stresses and service conditions of its intended environment.
custom heavy duty spherical bearing
Trust is an integral facet of utilizing custom components in any machinery, and establishing trust begins with choosing the right manufacturing partner. Companies that offer custom bearings often provide a wealth of experience and technical support, guiding the process from conceptualization to implementation. The presence of stringent quality assurances and performance testing further enhances the trustworthiness of these products. When customers are confident that their components will perform as needed, operational efficiency and safety are secured.
In terms of authoritativeness, manufacturers of custom heavy duty spherical bearings often hold certifications and comply with international standards, which cannot be understated. Adherence to standards such as ISO 9001 for quality management, or AS9100 for aerospace applications, reiterates a manufacturer's commitment to excellence and reliability. This adherence not only cements their standing in the market but also assures customers of the integrity and dependability of their products.
Ultimately, the choice of employing custom heavy duty spherical bearings is informed by a combination of expertise and specific needs of a project. The potential to enhance operational efficiency, equipment lifespan, and overall productivity makes these components a crucial investment. Companies that invest in understanding the nuances of their operational demands and partner with expert manufacturers gain a competitive edge, optimizing their equipment for today’s challenging industrial landscapes.
In summary, custom heavy duty spherical bearings are not just a product but a comprehensive solution engineered to overcome the limitations of traditional bearings under strenuous conditions. Their role in enabling robust and reliable equipment operation cannot be overstated, making them indispensable for industries that demand uncompromising standards and performance. As machinery and operations continue to evolve, these components stand as a testament to the power of innovation and engineering excellence.