Custom greasing of electric motor bearings stands as a pivotal process for ensuring the longevity and optimal performance of industrial machinery. Experience in maintaining electric motors reveals that neglecting this critical maintenance step can lead to premature motor failure, increased downtime, and costly repairs.
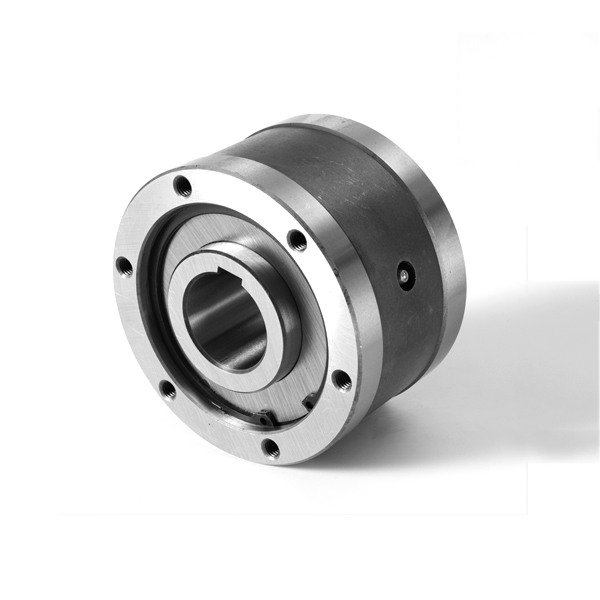
Electric motor bearings are precisely designed to support and distribute rotational loads efficiently. However, over time, these bearings are exposed to adverse conditions such as high operational temperatures, contamination from dust and debris, and moisture ingress. These elements can compromise the integrity of standard lubricants, making it essential to adopt a tailored greasing regimen.
An effective custom greasing plan commences with an in-depth analysis of the electric motor’s operational environment. This analysis should consider variables such as ambient temperature, humidity levels, and the presence of contaminants. Consultation with lubrication specialists can provide insights into selecting the ideal grease formulation that withstands specific conditions. For instance, motors operating in high-temperature environments may require synthetic greases with exceptional thermal stability.
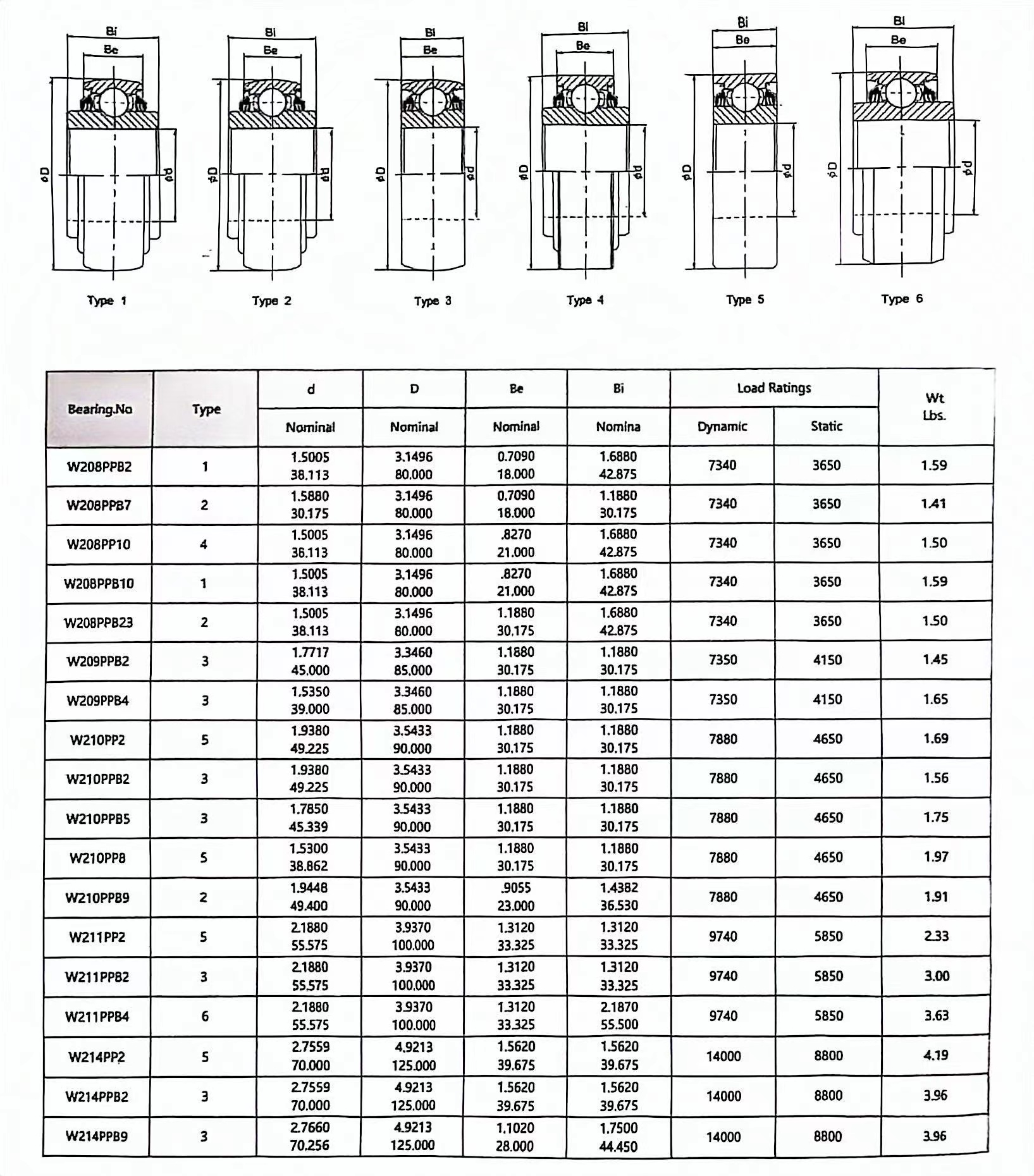
Expertise in bearing lubrication underscores the importance of selecting the appropriate grease consistency and viscosity. These attributes directly affect the ease of grease migration and film formation between bearing surfaces. Employing grease that is too thick may hinder rolling element motion, while overly thin lubricants might fail to maintain adequate separation between bearing surfaces, leading to increased contact and wear.
custom greasing electric motor bearings
Authoritative techniques in greasing electric motor bearings involve precision and accuracy. Bearing over-lubrication is a common mishap, often resulting from a well-intended but misguided approach to achieve thorough lubrication. Excess grease can not only result in leaking, which attracts contaminants, but also generate additional friction, causing heat buildup and potential motor damage. Adhering to manufacturer-specified quantities and intervals remains paramount for maintaining bearing health and ensuring peak motor performance.
Trustworthiness in maintaining electric motor bearings also calls for diligent monitoring and timely replenishment of lubricants. It is critical to establish a routine greasing schedule based on motor operating hours rather than a fixed calendar timeline. Condition-based monitoring, utilizing tools such as vibration analysis and infrared thermography, can offer predictive insights into bearing health and lubrication needs.
In the realm of product care, understanding the signs of inadequate lubrication is vital. Unusual noises, increased vibration, and elevated temperatures are common indicators that a bearing requires immediate attention. Prompt response to these warning signs, combined with a strategic greasing protocol, can effectively prevent untimely failures and extend motor life significantly.
Ultimately, the goal of custom greasing electric motor bearings is not merely to maintain function but to enhance motor efficiency, reliability, and lifecycle. By leveraging detailed environmental assessments, selecting appropriate lubricants, adhering to precise greasing techniques, and embracing a proactive maintenance mindset, businesses can secure sustained operational excellence and cost savings. Through this comprehensive approach, the intricate needs of each electric motor are met, and organizations can confidently drive forward without interruption.